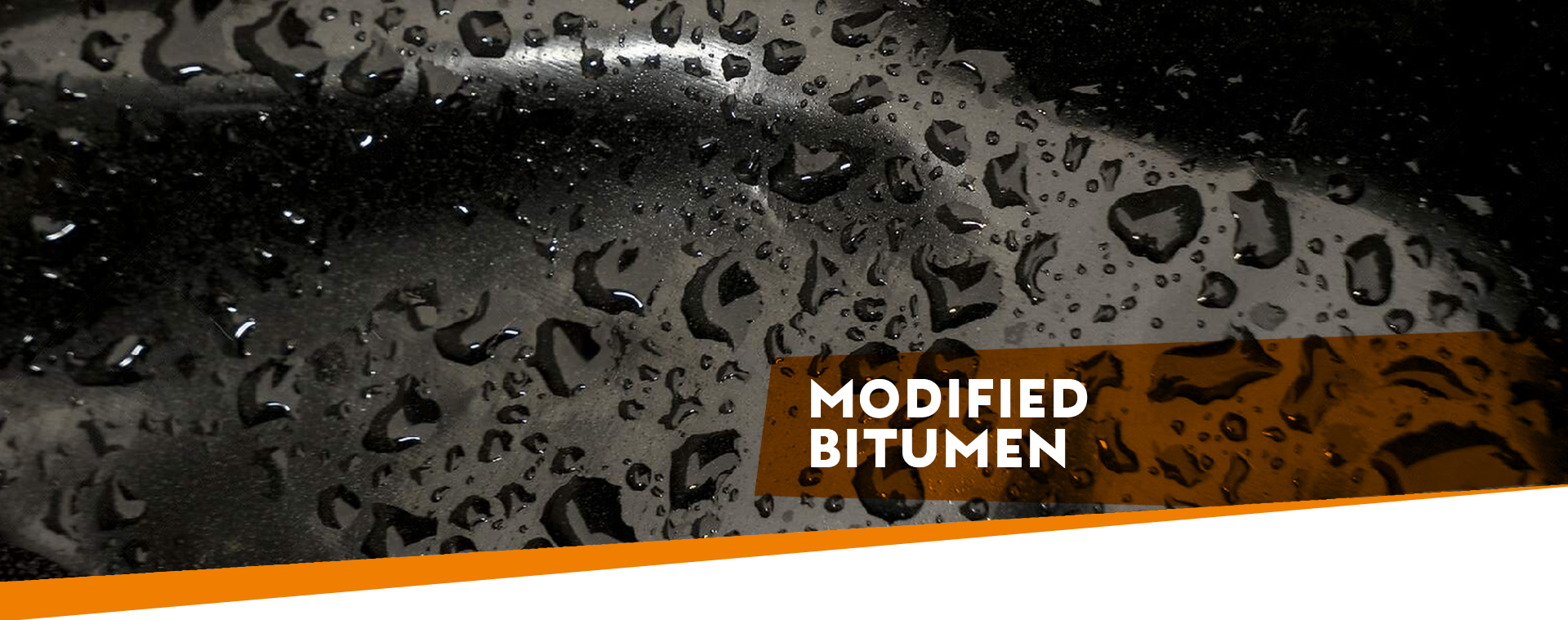
Modified Bitumen
Flexible roads tend to become soft during summer and breakable in winter due to high temperature variations. Due to heavy traffic loads on such roads, early development of distress issues can occur. In these situations, ordinary bitumen is not enough to overcome these issues. Modified bitumens are formulated with additives to improve their features and performance by changing such properties as their durability, resistance to ageing, elasticity and plasticity.
Modified Bitumen creates a better sealant and is more durable. This type of bitumen has become popular with commercial buildings and road systems because of its strength and resistance to inclement weather. It can also be used for residential roofing, for low sloped roofs.
Applications of Modified Bitumen
Since a bituminous mix prepared with modified bitumen has a higher stiffness modulus, enhanced fatigue life, better resistance to creep and higher indirect tensile strength, it is suitable as a wearing course, a binder course and overlay material on surfaces which are cracked and subjected to heavy traffic. Modified binders are also used for application like Stress Absorbing Membrane (SAM) for sealing of cracks, Stress Absorbing Membrane Interlayer (SAMI) for delaying reflection cracking, Porous Asphalt and Stone Matrix Asphalt (SMA). Modified bitumen performs better than conventional bitumen in situations, where the aggregates are prone to stripping. Due to their better creep resistance properties, they can also be used at busy intersections, bridge decks and roundabouts for increased life of the surfacing.
Our Modified Bituminous Product Range
1. Crumb Rubber Modified Bitumen
Crumb Rubber Modified Bitumen (CRMB) is made by the amalgamation of crumb rubber modifier and the chosen bitumen grade. The modifier works as an agent that strengthens the binder from the occurrence of any deformation when trying to maintain during low temperature, fatigue or thermal issues. CRMB is beneficial as it increases the life of a road by 1.5 to 2 times as compared to using a normal bitumen modifier. Our CRMB provides some unique properties different from bitumen binders like the strong adhesion reduces cracking, deformation, etc. It increases the stability of the material, homogeneity throughout the supply chain.
Research worldwide has shown that the addition of crumb rubber to bitumen produces binders with improved resistance to combat pavement distresses such as rutting, fatigue cracking, thermal cracking etc. It has also been demonstrated that use of crumb rubber modified binder’s leads to reduction of overlay thickness as well as reduce reflective cracking potential. This adequately demonstrates that CRMB is a superior binder which has immense application in highly trafficked National and State Highways of India.
Types of CRMB
CRMB 50, 55 and 60
There are 3 types of Crumb Rubber Modified Bitumen. CRMB 50 is best suitable for cold regions. CRMB 55 is used in moderate temperatures while CRMB 60 works best in hot regions with high temperatures.
Applications of Bitumen 115/15
- The resistance to fatigue is high.
- It is very cost effective.
- Strong resistance to thermal and changing temperature cracking.
- It gives a good experience in extreme climates.
- The Aging process slows down by mixing rubber with bitumen leading to increased lifespan.
- It gives protection from water damage due to the hard grade of asphalt formed.
Specification of CRMB ( E ) as per IRC SP 53 – 2002 & BIS I5462 – 2004
Designation | Grades and requirements | Test Method | ||
---|---|---|---|---|
Designation | Grades and requirements | Test Method | ||
------- | CRMB 50 | CRMB 55 | CRMB 60 | ------- |
Penetration @ 25°c | <70 | <60 | <50 | ISI 203 – 1978 |
Softening point, (R & B), C Min. | 50 | 55 | 60 | ISI 205 – 1978 |
Elastic Recovery of half thread in | 50 | 50 | 50 | ISI 5462 – 2004 |
Flash Point,°C Min | 220 | 220 | 220 | ISI 209 – 1978 |
Seperation difference in softening point, | 4 | 4 | 4 | ISI 5462 – 2004 |
Thin Film Oven Test (TFOT) on Residue | ||||
a. Penetration 25°C , Min % of original | 60 | 60 | 60 | ISI 203 – 1978 |
b. Increase in softening point,°C, Max | 7 | 6 | 5 | ISI 205 – 1978 |
c. Elastic Recovery of half thread in | 35 | 35 | 35 | ISI 5462 – 2004 |
Ductilometer at 25°C , % Min. |
2 Polymer Modified Bitumen
Polymer modified bitumen (PMB) is one of the specially designed and engineered bitumen grades that are used in making pavement, roads for heavy duty traffic and home roofing solutions to withstand extreme weather conditions. PMB is a normal bitumen with the added polymer, which gives it extra strength, high cohesiveness and resistance to fatigue, stripping and deformations, making it a favourable material for infrastructure. Pavements designed and constructed for heavy-duty traffic and extreme weather conditions require specially designed engineered Bitumen Grades. By changing the characteristics of normal bitumen with the addition of a polymer, either they are of elastomeric nature or elastomeric, we succeed to obtain bitumen that allows the mixture to be more cohesive, with much more strength and significant higher resistance to parameters like fatigue and permanent deformations for road pavements.
It is used for Wearing course & Binder courses like Semi dense Bituminous Concrete (SDBC), Dense Bituminous Macadam (DBM) and Bituminous Concrete (BC) or Asphalt Concrete (AC).
Types of Polymer Modified Bitumen
Type | General Purpose or Use | Generic Examples |
---|---|---|
Type | General Purpose or Use | Generic Examples |
Filler | Fill voids and therefore reduce optimum asphalt content. Meet aggregate gradation specifications. Increase stability. Improve the asphalt cement-aggregate bond. | Mineral filler Crusher fines Lime Portland cement Fly ash Carbon black |
Extender | Substituted for a portion of asphalt cement (typically between 20–35 % by weight of total asphalt binder) to decrease the amount of asphalt cement required | Sulphur Lignin |
Rubber | Increase HMA stiffness at high service temperatures Increase HMA elasticity at medium service temperatures to resist fatigue cracking Decrease HMA stiffness at low temperatures to resist thermal cracking | Natural Latex Synthetic latex (e.g., Polychloroprene latex) Block copolymer (e.g., Styrene-butadiene-styrene (SBS)) Reclaimed rubber (e.g., crumb rubber from old tires) |
Plastic | Polyethylene/Polypropylene Ethylene Acrylate Copolymer Ethyl-Vinyl-Acetate (EVA) Polyvinyl Chloride (PVC) Ethylene Propylene or EPDM Polyolefin | |
Rubber-Plastic Combinations | Blends of rubber and plastic | |
Fiber | Improving tensile strength of HMA Mixtures. Improving cohesion of HMA Mixtures. Permit higher asphalt content without the significant increase in the drain down | Natural: Asbestos Rock wool Manufactured: Polypropylene Polyester Fiberglass Mineral Cellulose |
Oxidant | Increase HMA stiffness after the HMA is placed | Manganese salts |
Antioxidant | Increase the durability of HMA mixtures by retarding their oxidation | Lead compounds Carbon Calcium salts |
Hydrocarbon | Restore aged asphalt cement to current specifications Increase HMA stiffness in general. | Recycling and rejuvenating oils Hard and natural asphalts |
Antistripping Agents | Minimise stripping of asphalt cement from aggregates | Amines Lime |
Waste Materials | Replace aggregate or asphalt volume with a cheaper waste product | Roofing shingles Recycled Tires Glass |
Specification of PMB as per BIS I5462 – 2004
Specification / Property | Grades and requirements | ||
---|---|---|---|
Specification / Property | Grades and requirements | ||
------ | PMB 40 | PMB 55 | PMB 120 |
Softening Point,°C (min) | <60 | <55 | <50 |
Penetration at 25°C | 30-50 | 50-90 | 90-150 |
Elastic Recovery of half thread, % ( min ) | 70 | 70 | 70 |
Separation, Difference in softening point,°C ( Max ) | 3 | 3 | 3 |
Advantages of Polymer Modified Bitumen
- Greater Rigidity
- Better resistance to permanent deformation
- Higher Resistance to spreading cracks
- Greater water resistance
- Much higher durability
- Enhances life of periodical maintenance and overlays by about 1.5 times as compared to conventional Bitumen.
- Lower susceptibility to temperature variations.
- Higher resistance to deformation wear and tear.
- Low glass transition temperature which gives excellent performance properties of pavement at low temperatures.
- Stiffer blend reduces rutting and stability at high temperatures.
- Enhances Dimensional stability and strength of pavement.
- Improves abrasion resistance of pavementImproves abrasion resistance of pavement.
- Improves Fatigue resistance.
- Reduces Oxidation and ageing resistance.
- Reduces structural thickness of pavement.
- Provides better adhesion between different aggregates.
- Delay cracking and reflective cracking.
Mittal Siddhi Infra Pvt. Ltd. is a prominent importer and supplier of Viscosity Grade Bitumen and different types of bitumen and petrochemical products based on international standards. We provide bitumen on an immediate basis and in bulk quantity for our Indian customers since the most usage of bitumen is in India’s roads.